Electric Motors commonly used in Electric Vehicles
Hello people. This article is about electric motors commonly used in electric vehicles. Following types of Electric Motors are most commonly used in Electric Vehicles
1. DC Series Motor
This motor has a high starting torque capability thus making it a suitable option for traction application. The advantages of this motor are easy speed control. It can also withstand a sudden increase in load.
These properties make it an ideal traction motor. These motors are used in Indian railways. The main drawback of DC series motor is high maintenance due to presence of brushes and commutators. This motor comes under the category of DC brushed motors.
Are you looking to start your business in the electric vehicle industry? We provide software development, web application development, mobile application development, charging stations management app, electric vehicle fleet management software development, cyber security and all software services. Please check our home page here https://iwheels.co/
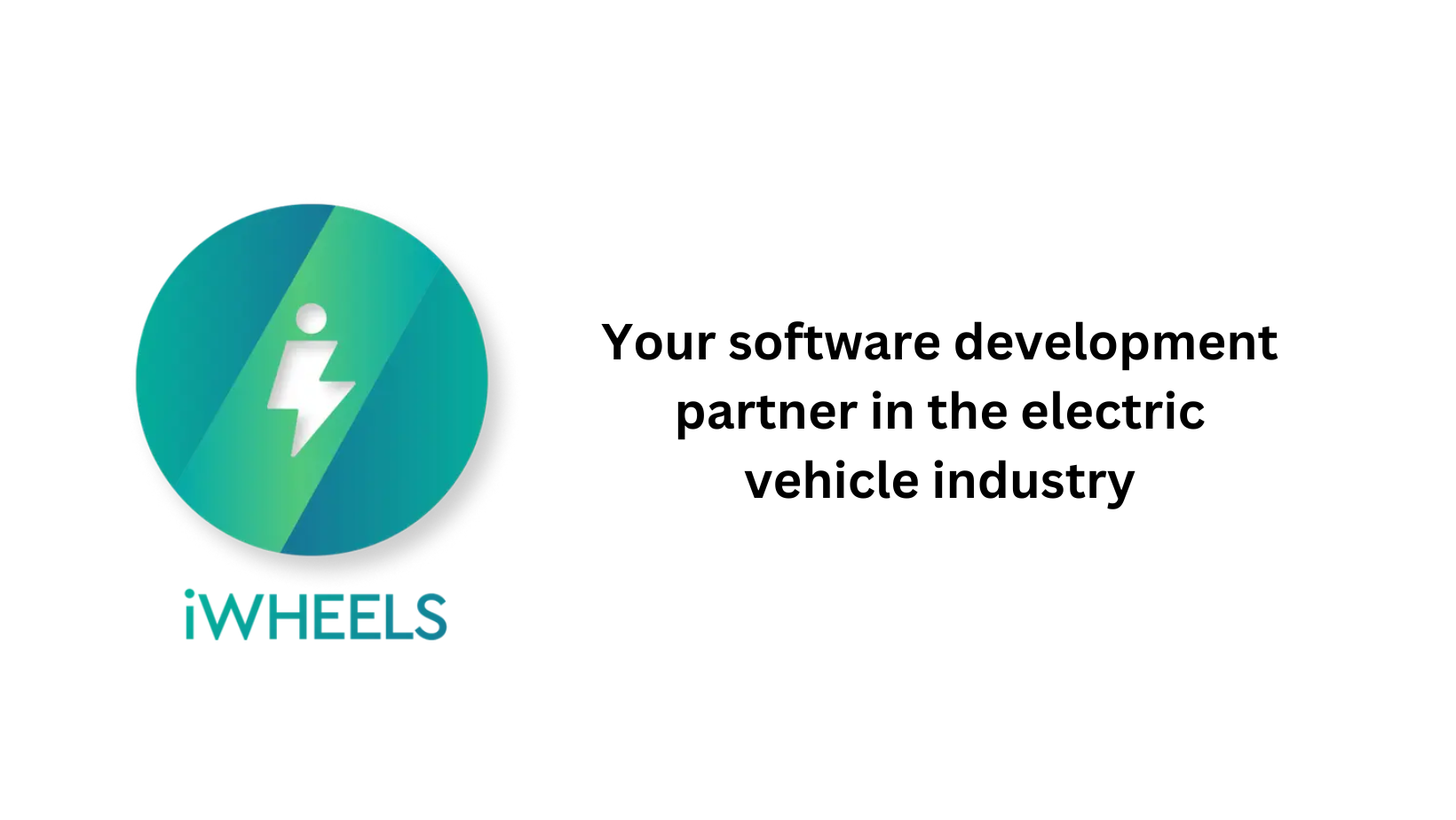
Ok. Let's get back to the article.
2. Brushless DC Motors
Brushless DC Motors are similar to DC motors with Permanent Magnets. It is called brushless because it does not have the commutator and brushes. The commutation is done electronically in this motor.
This characteristic of this BLDC motors make them maintenance free. BLDC motors have traction characteristics like high starting torque, high efficiency around etc.
These motors are suitable for high power density design approach. These motors are the most preferred motors for the electric vehicle application due to its traction characteristics.
BLDC motors are further classified into two types
i. Out-runner type BLDC Motor
The rotor of the motor is present outside and the stator is present inside. These are also called as Hub Motors because the wheel is directly connected to the exterior rotor. This type of motors does not require external gear system.
In a few cases, the motor itself has inbuilt planetary gears. It also eliminates the space required for mounting the motor. There is a restriction on the motor dimensions which limits the power output in the in-runner configuration.
ii. In-runner type BLDC Motor:
In this type, the rotor of the motor is present inside and the stator is outside like conventional motors. These motor require an external transmission system to transfer the power to the wheels.
Due to this, the out-runner configuration is little bulky when compared to the in-runner configuration. Many three- wheeler manufacturers like Goenka use BLDC motors.
Low and medium performance scooter manufacturers also use BLDC motors for propulsion. BLDC In-runner type motor is used in Ather Scooter.
3. Permanent Magnet Synchronous Motor
This motor is also similar to BLDC motor which has permanent magnets on the rotor. Similar to BLDC motors these motors also have traction characteristics like high power density and high efficiency.
The difference is that PMSM has sinusoidal back EMF whereas BLDC has trapezoidal back EMF. Permanent Magnet Synchronous motors are suitable for higher power ratings.
PMSM is the best choice for high performance applications like cars, buses. Despite the high cost, PMSM is providing stiff competition to induction motors due to increased efficiency than the latter.
PMSM is also costlier than BLDC motors. Most of the automotive manufacturers use PMSM motors for their hybrid and electric vehicles. For example manufacturers like Toyota Prius, Chevrolet Bolt EV, Ford Focus Electric, Zero motorcycles S/SR, Nissan Leaf, Hinda Accord, BMW i3, etc use PMSM motor.
4. Three Phase AC Induction Motors
Induction motors do not have high starting toque like DC series motors under fixed voltage and fixed frequency operation. But this characteristic can be altered by using various control techniques like FOC or v/f methods.
By using these control methods, the maximum torque is made available at the starting of the motor which is suitable for traction application. Squirrel cage induction motors have a long life due to less maintenance.
Induction motors can be designed up to an efficiency of 92-95%. The drawback of an induction motor is that it requires complex inverter circuit and control of the motor is difficult.
Tesla Model S is the best example to prove the high performance capability of induction motors compared to its counterparts.
By opting for induction motors, Tesla might have wanted to eliminate the dependency on permanent magnets. Even Mahindra Reva e2o uses a three phase induction motor for its propulsion. Major automotive manufacturers like TATA motors have planned to use Induction motors in their cars and buses.
The two-wheeler manufacturer TVS motors will be launching an electric scooter which uses induction motor for its propulsion. Induction motors are the preferred choice for performance oriented electric vehicles due to its cheap cost.
The other advantage is that it can withstand rugged environmental conditions. Due to these advantages, the Indian railways has started replacing its DC motors with AC induction motors.
5. Switched Reluctance Motors
This is a category of variable reluctance motor with double saliency. These are simple in construction and robust. The rotor of the SRM is a piece of laminated steel with no windings or permanent magnets on it.
This makes the inertia of the rotor less which helps in high acceleration. The robust nature of SRM makes it suitable for the high speed application. SRM also offers high power density which are some required characteristics of Electric Vehicles. Since the heat generated is mostly confined to the stator, it is easier to cool the motor.
The biggest drawback of the SRM is the complexity in control and increase in the switching circuit. It also has some noise issues. Once SRM enters the commercial market, it can replace the PMSM and Induction motors in the future.
Hope this article on electric motors commonly used in electric vehicles is useful to you. To read about jobs in the Electric Vehicle Industry, please visit Job opportunities in Electric Vehicle Sector and its Charging Infrastructure industry